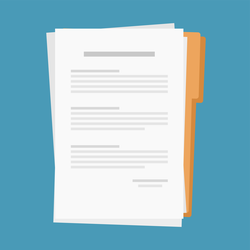
The question of “What’s the difference between Process vs procedure” is a troubling one. While you’d think such a question would be clear cut, so it’s perhaps a surprise why many struggle with it.
You’ll often find many businesses using the terms interchangeably, which can add further confusion.
While the ISO standard provides some guidance, you’ll find many businesses still calling processes – procedures, work instructions processes, and procedures a process.
The fact is that BOTH process and procedure can add such huge value to an organization and they both have their own place. As a result, it’s clear that the business needs to have each well defined to get the best out of them.
In this article, we’ll try to take a look at the difference between Process vs Procedure.
What is the definition of Process vs Procedure?
If you’ve just come for a simple definition then I’d suggest that we can paraphrase ISO 9001 and come up with something like the following:
Process
A process is a series of related tasks that collectively turn input into an output.
In other words, a process is what we do.
Example: Assembling the parts of an automobile to form a finished vehicle.
Procedure
A procedure is a specified way of carrying out a process (either in part or in whole). In other words, a procedure is how we do a process.
Example: The detailed instruction document that describes precisely how to assemble the automobile. This clearly identifies the steps to be taken, responsibilities, tools/documents, standards to adhere to use etc.
So they both separately exist within a business, but have different roles to play
Process vs Procedure: What’s the real Difference?
So why don’t we stop at our simple definition above?
Interestingly there has been so much debate around the definitions even the ISO standards looked to clarify it at one stage (you can read their ever so fascinating whitepaper on it here https://www.bsigroup.com/LocalFiles/en-IN/Resources/Whitepaper-Difference-between-a-procedures-and-a-process-approach-in-the-new-ISO-standards-418-KB.pdf)
So the difference between Processes and Procedures is hopefully clear enough, but people in the workplace still get confused. This tends to drive a plethora of needless documents that does little else other than put the organization in a document headlock.
Driving the real difference between the two can be helped enormously when you’re looking at documenting what you do in your workplace.
In ISO 9001, the standard demands that you document processes within the quality management:
More specifically, these are highlighted as:
- Processes for managing the organization
- processes for managing resources
- Operational processes
- Processes relating to measurement, analysis and improvement
A bit more detail on Process vs Procedure
Let’s take a look at what Process vs Procedure consists of in a bit more detail:
Process
- Input – what you start your process with – this could be raw material, a customer order etc
- Process steps – usually diagrammatically represented by a flow chart – this indicates the steps to be followed
- Output – what the input + process steps result in. This could be an asset you can sell to your customer, it could be a completed document – whatever it is it’s the finale of the process.
Procedure:
- Sequence/Steps to be taken (this usually includes physical activities + Documentation to complete), this may make reference to the process instruction
- Roles and responsibilities
- Standards and specifications to adhere too.
In documenting these effectively, a business can derive value by identifying what processes exist and how they fit together.
Now when we look at it from a business context, process and procedure serve two quite different purposes.
Process
As you can see, a process is more surface-level. It’s something that can be easily captured using a flow chart and then used by management to analyze the efficiency of their business.
Procedure
A procedure, on the other hand, focuses on things like precise instructions, roles and responsibilities, standards to be adhered to and records that must be kept.
What’s crucial is it’s pointless producing either of them just for the sake of creating a document, the very purpose of processes and procedures is that they are there to help your employees and help your business achieve its objectives in a repeatable fashion.
Documenting Process vs Procedure
Unsurprisingly, processes and procedures tend to be documented in different ways.
A procedure is typically far more detailed meatier document (you’ll probably have seen Procedures captured in Word Documents), processes tend to be captured in much simpler methods such as flow charts or value stream maps.
Without documenting both processes AND procedures, continuous improvement is made extremely difficult. Improvement begins with understanding what you do and how you do it, and therefore mapping this out becomes imperative.
Why a business should document both processes and procedures
So the real value of capturing process and procedures is twofold:
- It details and describes how the business functions
- It captures information to drive efficiency and effectiveness
Given the importance of procedures, it’s unsurprising that many businesses want to skip the step of capturing processes.
However, without effectively documenting both processes and procedures, a business puts itself increases various risks such as non-conformance.
Enforcing processes and procedures.
Many organizations spend an incredible amount of time documenting their processes and procedures; the downside of this is that without proper attention and focus you can create management systems that no-one ever looks at.
So, how can you guarantee staff use and follow them?
There are three guiding principles.
- Make them useful
- Make them simple
- Make them accessible
Documented processes AND procedures are vital to any business.
Hopefully, by now you can ascertain the difference between the two documents and explain why they are vital in your management system. However, before we finish, let’s run over some of the key benefits:
- Provides a standard to work to which drives consistency
- Provide a basis from which to conduct improvements from.
- Supports compliance
- Provide inputs into efficiency reviews
- Places knowledge of operations into the business system rather than just the heads of operators (what would happed if someone left the organization and they had all the knowledge of how things were done?!)
Capturing and documenting a process ensures it becomes repeatable. It also enables it to be systematically reviewed and improved. This is a fundamental principle in any Quality management system.
Summary
We hope you enjoyed this delve into processes and procedures. If you’ve got a question or some feedback on the article or even how you use processes and procedures in your organization then we’re all ears. We’d love your feedback below or a message on Twitter!