
The red tag process (which is often associated with the SORT activity within 5s) incorporates visual management through the use of a “red tag” form or label identifying items that have been flagged for removal from a work area.
Red tagging can help identify items that shouldn’t be in a workplace, move them so that they can be reviewed, and provide mechanisms of disposal where they are unclaimed.
In this article, we’ll be looking at the red tag process; we’ll be covering
- What is a red tag process
- Example Red Tag
- What is the red tag area
- What are red tag events
- What should an organisation do with unclaimed items
- Benefits of red tag process
- Common issues with red tag process
What is the Red Tag Process
Businesses accumulate “stuff,” teams get formed/disbanded, departments get moved, and activities occur where workers are temporarily located.
All of these things can drive equipment and other paraphernalia to be left in a work area, which, when compiled with a lack of housekeeping, can make work areas untidy and inefficient.
If you read our “What is 5s” article, you’ll see that one of the process steps is SORT, where the work area is reviewed where the goal is leaving behind only what is absolutely required to perform the task designated for that area.
Part of the challenge of this process step is that you might find items where there is uncertainty over
- The use of the item
- The owner of the item
This is where the red tag process comes in.
The red tag process has a series of steps that include:
1/ Item identification
A work area is reviewed, and unused items are identified.
2/ Review items
Items are recorded and often photographed so their presence can be communicated to the organization.
At this stage, items are classified:
a) Needed (and retained in the area)
b) Belongs in another known area (item is often collected)
c) Unknown
Many organizations will amalgamate b & c, tagging both sets of items.
3/ Classify the item as ‘red tagged.’
This involves physically marking the item with a ‘red tag’ and placing the item in the red tag review area.
An example red tag can be seen below:
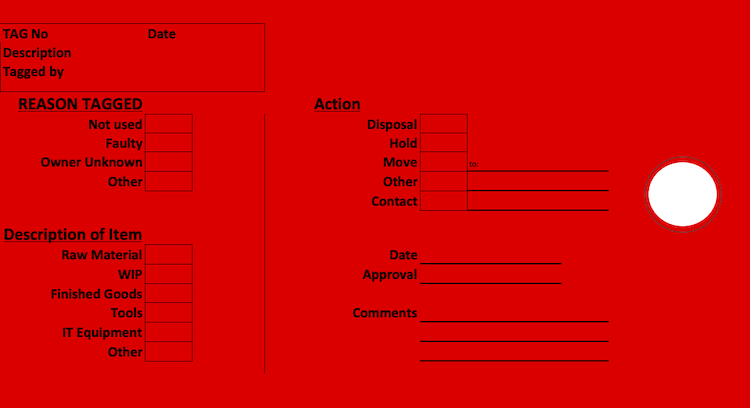
The red tag then acts as a visual management artifact, indicating that the item has been:
- Found
- There may be uncertainty over who ‘owns’ the item/use or where it should belong
- That the item will be disposed of by the date articulated on the tag.
At this stage, the organization might review any asset or ID number on the equipment to help identify it.
It’s common for the red tag area to feature some form of tracker, often a formatted dry wipe board that enables the tracking of items placed within the zone.
An example can be seen below:
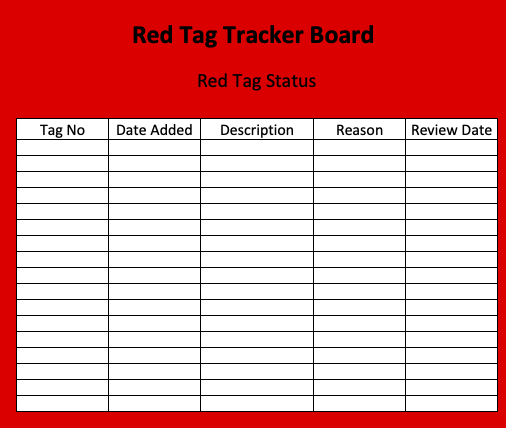
4/ Allocate a period of time for it to be claimed or a use identified
Most businesses will have a particular time envelope where items remain in the red tag area for review; this could be a week, a fortnight, or a month.
In most cases, the review period is likely to be short, with all tagged items likely to have the same review period.
5/ Discuss ownership/use
Once tagged items are moved to the red tag area – they will either be
a) Claimed
b) Unclaimed
Where an item has been claimed, it will usually follow a route where
- The item will be removed from the red tag area and placed somewhere different from the area where it was found.
- There will be a discussion on why the item should be returned to where it was found.
It’s not unusual to see disagreement.
You might find people have become attached to a piece of equipment as it’s of great value once or twice a year; some may see an item of equipment as de-risking an activity (even though it’s never been used).
In short, there is often debate.
Ultimately, a decision will need to be made on whether the item remains or is disposed of. This may require a level of senior involvement/sign-off.
Many organizations require a senior sign-off in order to remove the red tag.
6/ Return the item to the work area or dispose of it
The final part of the red tag process is to either:
- Remove the tag & return the item to the work area it was found
- Remove the tag and place the item in another work area where it can provide value
- Scrap off or sell the item
Example Red Tag
Example red tags can be seen below:
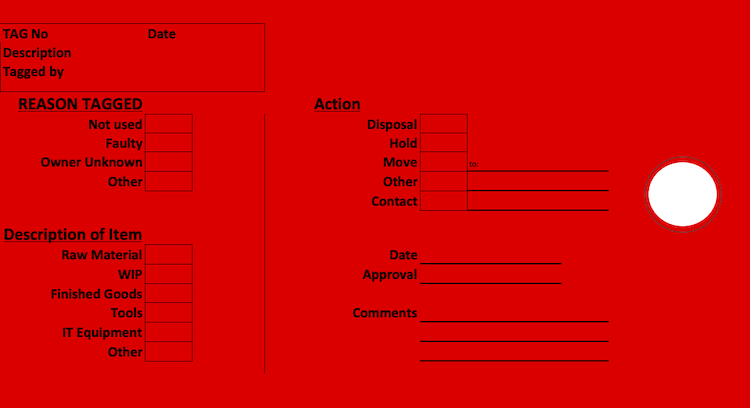
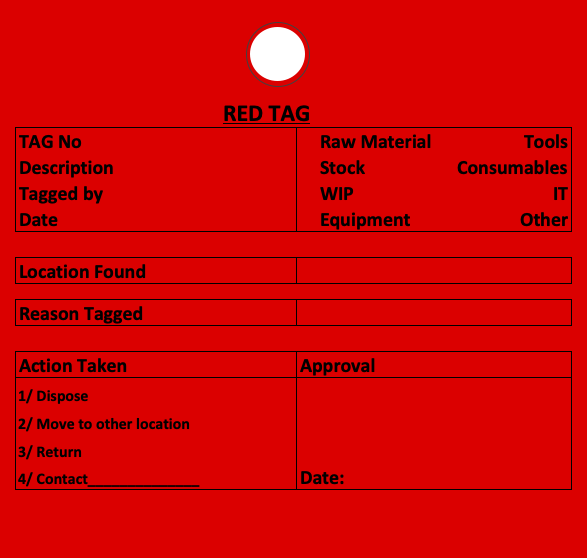
What is the Red Tag Area
The red tag area is a location within the business where tagged items are stored. It has several characteristics:
- This area should be segregated from production areas to prevent red-tagged items from taking up space or being incorrectly utilized.
- It should be kept tidy, facilitating tagged items to be easily reviewed.
- It should be periodically reviewed to ensure tidiness.
- Items should be maintained in line with red tag dates.
- Red tag areas require rules, processes, and ownership in order to be effective.
- Items should not be thought of as being scrapped – they are likely to have value to the organization; scrapping/selling should be a last resort.
What are red tag events?
A red tag event is simply where the 5s “sort” stage is carried out, and team members are engaged with reviewing items in the work area.
This can be specific to a 5s program or carried out independently.
Items in the area are sorted, and items that require tagging are done so and subsequently moved to the red tag area.
What should an organization do with unclaimed red tag items?
As a result of the process, you’ll probably find yourself with some items leftover in the red tag area that has not been claimed.
So, what are your options when this happens?
Every business will have its own process (and may depend on the sort of equipment unclaimed); options include:
- Retaining the items
- Scrapped/placed in the trash
- Send the item to be recycled
- Sell the item
- Give to charity
- Allow them to be purchased by employees
Benefits of red tag process
There are numerous benefits associated with the ret tag process; these include:
- Simple to use
- Part of “sort” process step within 5s
- Wide engagement of staff who can assist with the process
- Can help eliminate issues around the “Sort” part of the process
- Can protect a work area from unnecessary scrapping of equipment prior to review.
- It prevents incorrect equipment from being used.
- A tidy red tag area facilitates an effective review and recovery of lost items.
Issues with red tag process
- The red tag area becomes a dumping ground for items, with the final red tag step not being followed.
- Agreement about whether an item should be returned to the area cannot be settled.
- Items that are only used intermittently but are vital to the process may be removed in error.
- Failure to apply label/red tag and items become stranded not knowing where they were found or what process they could relate to.
- The red tag area becomes messy and difficult to manage.
- Lack of senior ownership where there is a dispute over items tagged.
- Items are removed from an area and placed in the red tag area without tagging.
- Staff are not trained effectively in the process resulting in errors.
- Effort is not sustained.
Summary
The red tag process is a simple yet effective method of sorting through equipment/tools in a work area, moving items that do not belong there, and using visual management so they can be reviewed later on.
Have you applied red-tagging in your company? How did the process go? What were the main benefits? Did you face any issues?
We’d love to hear from you; you can reach us via Twitter or via the comments section below.
This article is part of our Lean guide.